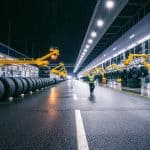
Резина, которая является полимером
Пластик: Пластик обладает свойствами пластмассы.
Резина и силикон — в чем разница
Современный рынок эластомеров полон различных материалов, включая резину и силикон. Их часто сравнивают друг с другом, пытаясь определить, чем они отличаются, какой из них лучше, прочнее, долговечнее. Что отличает резину и силикон от пластмасс, так это их эластичность и упругость.
Это эластичный материал, образующийся в результате вулканизации натурального или синтетического каучука. Сырьем для первого является латекс (млечный сок каучукового дерева Gevea brazilica, основным компонентом которого является углеводород под названием полиизопрен). Второй производится из таких углеводородов, как бутадиен, изопрен, неопрен, стирол, хлоропрен и других, с использованием технологии полимеризации/сополимеризации.
Вулканизация — это технологический процесс, в котором натуральный/синтетический каучук взаимодействует с вулканизующим агентом: серой, пероксидами, соединениями аминного типа, оксидами металлов, другими веществами. Кстати, вулканизующим агентом могут быть не только вещества, но и физические явления, например, излучение.
Его действие направлено на сшивание молекул каучука и создание однородной пространственной сети с целью повышения прочности, твердости, эластичности и снижения уровня пластичности, набухания и растворимости в органических растворителях.
Состав
Для производства каучука используются резиновые смеси различных марок, состав которых представлен:
- натуральные/синтетические каучуки
- вулканизующий агент;
- вулканизующие агенты: магний, оксиды свинца, полисульфиды;
- антиоксиданты: альдол, неозон Д, воск, парафин — добавляются в резиновые смеси для замедления скорости старения резины;
- пластификаторы: битум, вазелин, парафин, стеариновая кислота, растительные масла и другие — для повышения эластичности резины;
- наполнители: активные (оксид цинка, кремниевая кислота) и неактивные (барит, мел, тальк).
- Регенерат — продукт, получаемый при переработке старых резиновых изделий и резиновых отходов;
- Красители, которые могут быть органическими или на минеральной основе.
Что такое силикон?
Силикон — это полимер, который является разновидностью синтетического каучука. Ключевое различие между каучуком и силиконом заключается в том, что первый основан на водороде, а второй — на чередовании атомов кремния и кислорода.
Кремниево-кислородные связи являются более высокоэнергетическими, чем водородные. Это делает силикон более устойчивым к высоким температурам, чем резина и многие другие эластомеры.
Силикон синтезируется с использованием методов гидролитической поликонденсации или полимеризации.
Состав
Силиконовая смесь, как и другие резиновые смеси, также является многокомпонентной. В его состав входят:
- синтетический каучук — основа композиции;
- армирующего агента, отвечающего за обеспечение прочности композиции после отверждения;
- пластификатор, придающий эластичность;
- вулканизатор, придающий составу вязкость
- краситель — для придания смеси определенного цвета.
Кроме того, в состав смесей могут входить определенные наполнители для придания им определенных свойств. В состав силиконовых герметиков также входят праймеры, повышающие степень адгезии.
Преимущества и недостатки
- стойкость к высоким температурам, проявляющаяся в структурировании и сохранении всех технических и эксплуатационных свойств в широком диапазоне температур — от -60 оС до +200 оС, а для морозостойких силиконов — от -100 оС до +300 оС
- химическая инертность ко многим агрессивным веществам: пресная/морская вода, озон, спирт, минеральные масла, бензин, слабые растворы кислот/щелочей и др;
- устойчивость к внешним воздействиям, таким как радиация, ультрафиолетовое излучение, электрические разряды и поля;
- устойчивость к вредным микроорганизмам, насекомым и грызунам;
- нетоксичность, что позволяет использовать силиконовые изделия/детали во всех отраслях промышленности;
- долговечность;
- отличные электрические свойства: при температурах выше +100°C силикон превосходит другие эластомеры в этом отношении.
Что такое пластик
Пластик — это полимерный материал, которому можно придать форму и сформовать под воздействием тепла и давления. Это свойство известно как пластичность. Это синтетический полимер. Пластичность пластика позволяет придавать ему различные формы.
Кроме того, небольшой вес пластика аргументирует его использование в производстве различных устройств. Пластмассы обладают низкой плотностью, плохой электропроводностью, прозрачностью, ударопрочностью и т.д. Пластмассы очень стабильны и имеют низкую скорость разложения.
Существует широкий спектр пластмассовых полимеров. Эти пластмассы можно классифицировать по нескольким различным параметрам. Мы можем классифицировать пластмассы по химическим свойствам, физическим свойствам, химической структуре, методам синтеза и т. д. Д.
Некоторые коммерчески важные пластмассы включают полиэтилен, полипропилен, полистирол, ПЭТ, ПТЭФ и т. Д. В процессе производства этих видов пластмасс в реакционные смеси добавляются определенные химические соединения. Эти химические вещества включают стабилизаторы (для обеспечения длительного срока хранения полимеров), наполнители (для улучшения эксплуатационных характеристик), пластификаторы (для улучшения реологии) и т.д. и т.п. Иногда также добавляются красители для получения привлекательного цвета конечного продукта. Эти добавляемые извне соединения называются добавками.
Существует множество применений пластмасс практически во всех областях, включая медицину, текстиль, продукты питания и напитки (в качестве упаковочного материала).
Что такое резина
Каучук — это эластичный материал, который добывается из каучуковых растений или синтезируется из нефти. Существует два вида каучука: натуральный и синтетический. Каучук очень хорошо известен в промышленности благодаря своей эластичности, ударопрочности и т.д. Каучук используется для производства различных изделий.
Натуральный каучук состоит из полимеров изопрена и воды, а также нескольких других соединений. Основным компонентом натурального каучука является полиизопрен. Это полимерный материал (эластомер), присутствующий в натуральном каучуке. Натуральный каучук получают из латекса каучукового дерева. Этот латекс молочный и вязкий. Он представляет собой суспензию. Этот латекс может быть получен из частей, близких к коре дерева.
Натуральный каучук подвержен вулканизации из-за наличия двойной связи в основной полимерной цепи. Вулканизация — это процесс образования поперечных связей между полимерными цепями с использованием серы в качестве сшивающего агента. Вулканизированный каучук более жесткий и прочный, чем натуральный.
Рисунок 2: Структура полиизопрена в натуральном каучуке
Синтетические каучуки производятся из нефтяных масел или природного газа. Синтетические каучуки производятся на химических заводах с использованием нефтехимических продуктов в качестве исходного сырья. Например, в результате реакции ацетилена и соляной кислоты образуется полихлоропрен — разновидность синтетического каучука.
Существует множество различных продуктов, получаемых из каучука. Например, обувь, автомобильные шины, водонепроницаемая одежда, воздушные шары, защитные перчатки и другие.
Что такое синтетический каучук
Синтетический каучук — это искусственный каучук. Сырье, используемое для производства синтетического каучука, в основном получают в качестве побочных продуктов нефтедобычи. Для синтеза синтетических каучуков используются методы растворной или эмульсионной полимеризации. В отличие от натурального каучука, свойства этих каучуков могут быть адаптированы к конечным требованиям с помощью различных методов полимерной химии. Например, мы можем разработать синтетические каучуки с отличной устойчивостью к атмосферным воздействиям, химическому воздействию, температуре и растворителям.
Существует более 20 различных сортов синтетического каучука с различными химическими и физическими свойствами, отвечающими требованиям конечного продукта. Некоторые распространенные виды синтетического каучука включают стирол-бутадиеновый сополимер (SBR), нитрильный каучук (NBR), неопрен (CR), этилен-пропилен-диеновый мономер (EPDM), силиконовый каучук, бутилкаучук (IIR) и т.д. Каждый каучук обладает своими уникальными свойствами. Например, EPDM более популярен благодаря своей атмосферостойкости, в то время как NBR обладает самой высокой маслостойкостью. В целом, если сравнивать свойства синтетического каучука со свойствами натурального, синтетические каучуки более устойчивы к воздействию масел, некоторых химических веществ, кислорода и озона, атмосферных агентов, а также демонстрируют устойчивость в более широком диапазоне температур.
Разница между натуральным и синтетическим каучуком
Определение
Натуральный каучук: Натуральный каучук — это природный биосинтетический полимер, получаемый из дерева под названием Hevea Brasiliensis.
Синтетический каучук: Синтетический каучук — это искусственные полимеры, полученные в контролируемых условиях.
Синтез
Натуральный каучук: Натуральный каучук, как следует из названия, возникает естественным образом в клетках растений.
Синтетический каучук: Синтетический каучук синтезируется из побочных продуктов нефтепереработки с использованием методов растворной или эмульсионной полимеризации.
Мономер
Натуральный каучук: Мономеры включают цис-1,4-изопрен.
Синтетический каучук: Мономеры в каждом типе синтетического каучука разные.
Натуральный каучук: Содержание полимеров или качество латекса сильно варьируется и зависит от клона, географической зоны, погоды, типа почвы и содержания некаучука в латексе.
Синтетический каучук: Высококачественный каучук с постоянным содержанием полимеров может быть произведен с очень низким уровнем примесей.
Наличие антиоксидантов
Натуральный каучук: Антиоксиданты присутствуют в природе.
Синтетический каучук: Антиоксиданты отсутствуют (их необходимо добавлять извне).
свойства
Натуральный каучук: Свойства натурального каучука трудно модифицировать.
Синтетический каучук:Свойства синтетических каучуков могут быть изменены в соответствии с характеристиками конечного применения.
Arayapranee, Wanvimon и Harry L. Ремпель. ‘Влияние полярности на взаимодействие наполнителя с резиной и свойства композитов из натурального каучука, наполненных кремнеземом’. Журнал Полимеры 2013 (2013): 1-9. Web. Хофер, Райнер. Устойчивые решения для современной экономикиКембридж, Великобритания: RSC, 2009. печать. Уилан, Тони. Словарь по технологии полимеровЛондон: Чепмен и Холл, 1994. печать. Изображение любезно предоставлено: ‘EPDM-Keltan’ Gmhofmann — собственная работа
Синтетические каучуки
Рассмотрим подробнее синтетические каучуки. Эти соединения представляют собой синтетические полимеры, которые вулканизируются с образованием резины. Известно, что синтетические каучуки составляют большинство эластомеров. Синтетический каучук, или полибутадиен, получают в результате полимеризации бутадиена-1,3.
Первоначально для этой реакции использовался натриевый катализатор. В настоящее время для стереоспецифического присоединения используются бутиллитиевые катализаторы — катализаторы на основе комплексных соединений титана, неодима и никеля.
Классификация и свойства синтетических каучуков
Существует классификация синтетических каучуков в зависимости от их применения. Соответственно, различают:
-резины общего назначения — используются в производстве изделий, где требуется гибкость.
-резины специального назначения — используются в производстве изделий, где, помимо гибкости, требуется устойчивость к кислотам, щелочам и различным растворителям.
Синтетические каучуки обладают рядом важных и отличительных свойств. Например, каучук очень хорошо плавает в воде благодаря своему малому весу и нерастворим в воде, что делает его особенно подходящим для производства водостойких изделий. Синтетические каучуки растворимы в бензине, бензоле, эфирах и т.д. — Это делает его пригодным для использования в качестве клея. Возможность использования СК в качестве изоляционного материала обусловлена тем, что он не является проводником электричества и газов. Синтетический каучук сохраняет свои свойства при регулярной деформации. Материал также является достаточно гибким.
Рассмотрим основную технологическую схему полимеризации изопрена при производстве СКИ-3.
Изопрен и инертный растворитель закачиваются в смеситель 1, где происходит интенсивное перемешивание в течение 1 минуты при температуре от — 5 до 10°С для предотвращения образования значительного количества полимера. Изопрен с помощью центробежного насоса 2 направляется в батарею полимеризаторов 3, состоящую из четырех-шести блоков. С помощью дозирующего насоса раствор катализаторного комплекса направляется в первый полимеризатор. Полимеризационная смесь перетекает из одного аппарата в другой под действием силы тяжести из-за разницы давлений. Из последнего полимеризатора полученная масса поступает в смеситель 4. В смеситель 4 также подается пробка и раствор антиоксиданта для прерывания процесса полимеризации. После смесителя 4 реакционная масса направляется в колонну 5, где промывается водой. Затем смесь поступает в большие резервуары, не показанные на схеме, предназначенные для получения однородного состава. После них смесь поступает в дегазатор 6, где изопрен и растворитель отделяются с помощью жесткого пара.