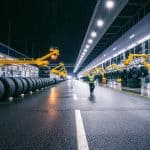
Каковы свойства резины
Резина широко используется благодаря своей эластичности, долговечности и устойчивости к воздействию масла и бензина. Даже в обычном легковом автомобиле используется 200 видов резиновых деталей. К ним относятся шланги, приводные ремни, втулки, рукава и т.д.
Список тематических статей
Каждый человек в той или иной степени соприкасался с резиной в своей жизни, и чаще всего с детства. Резина — это эластичное вещество, которое получается после реакции вулканизации как натурального, так и синтетического каучука. Резиновый материал, также известный как ‘вулканизат’, представляет собой эластомер с трехмерной, сшитой структурой, образованной путем сшивания макромолекул каучука химическими связями различной природы.
Как упоминалось выше, резина по своей природе является эластомером, что означает, что, в отличие от обычных пластмасс, она способна возвращаться к своей первоначальной форме и размерам после снятия нагрузки.
Получение
Резина в современной промышленности создается в основном путем вулканизации резиновых смесей, которые имеют довольно сложный состав. Основным ингредиентом и основой будущей резины является каучук, который может составлять до 60 процентов состава. Другие ингредиенты включают вулканизаторы, ускорители, активаторы, наполнители, антислеживающие агенты и пластификаторы. Помимо этих основных ингредиентов, в состав резиновой смеси могут входить и другие химические вещества, такие как регенераторы, модификаторы, красители, порофоры, ароматизаторы и т.д. Вся резиновая смесь может состоять из 20-30 веществ.
Конкретный каучук, который будет составлять основу резины и других компонентов в составе смеси, выбирается исходя из назначения, условий эксплуатации и других требований к резиновому изделию. Свойства изделия зависят от технологического процесса, который будет использоваться для переработки, а также от экономических и других факторов.
Технологические процессы производства изделий из данного материала включают смешивание каучука с другими ингредиентами резиновой смеси в смесителе или вальцовочном станке, приготовление резиновых полуфабрикатов, резку, сборку и другие операции последующей обработки, а также последующую вулканизацию изделий. Полуфабрикатами могут быть профили, полученные методом литья под давлением (аналогично экструзии пластмасс); листы, полученные методом каландрирования; прорезиненные ткани; корд и т.д. Прямая вулканизация происходит в реакторах периодического действия, таких как прессы, котлы, циклические автоклавы, или в автоклавах непрерывного действия, таких как туннельные, барабанные и другие автоклавы.
Благодаря высокой пластичности исходного материала, размеры и форма заготовки формируются и корректируются в процессе вулканизации. В этом процессе широко используются вулканизационные прессы, а также машины для литья под давлением. В этих процессах вулканизация и вулканизация совмещены в одной технологической операции. Основным вулканизующим агентом в каучуках является элементарная сера, обычно вводимая в количестве нескольких процентов по весу смеси. Смеси с высоким содержанием серы от 30 до 50 процентов дают эбонитовые продукты или полупродукты.
Состав каучука
Каучук представляет собой сложную смесь различных компонентов, каждый из которых играет определенную роль в формировании его свойств (рис. 6). В основе каучука лежат каучук. Основным вулканизирующим агентом является сера.
Рис. 6 Составные части каучука
Вулканизирующие агенты (сера, оксиды цинка или магния) принимают непосредственное участие в образовании (оксиды серы, цинка или магния) принимают непосредственное участие в образовании поперечных связей между макромолекулами. Каучук может содержать от 7 до 30 %.
Наполнители В зависимости от их воздействия на десны, они делятся на активныерезиновые наполнители, которые увеличивают твердость и прочность резины и тем самым повышают ее износостойкость, и инертныекоторые добавляются в состав резины для удешевления ее стоимости.
Пластификаторы входящие в состав каучуков (8 — 30%), облегчают их переработку, повышают эластичность и морозостойкость.
Антиоксиданты замедляют процесс старения резин, препятствуют присоединению кислорода. Кислород способствует разрушению макромолекул каучука, что приводит к потере эластичности, хрупкости и появлению сети трещин на поверхности.
Красители выполняют не только декоративную функцию, но и замедляют световое старение, поглощая коротковолновую часть света. Наиболее распространенные сорта натурального каучука — янтарного и светлого цвета.
Обычная классификация и номенклатура синтетических каучуков по. мономераммономерам, используемым при их производстве (изопрен, бутадиен, бутадиен-стирол и т.д.), или по характерной группировке (атомам) в основной цепи или боковых группах (например. полисульфидные, уретановые, силиконовые), фторкаучуки.
Получение и применение каучуков
Синтетические каучуки более широко используются в производстве резин и характеризуются разнообразием своих свойств. Синтетические каучукиКаучуки перерабатывают из спирта, сырой нефти, попутных газов нефтяной промышленности, природного газа и др. (рис. 7).
Рис. 7 Схема производства синтетических каучуков
СКБ — Бутадиеновый каучук, чаще используется в производстве специальных каучуков (см. рис. 8).
Рис. 8 Прокладки — гибкие уплотнения трубчатого или другого сечения
SKS — Стирол-бутадиеновый каучук. Резина СКС-30стирол-бутадиеновый каучук — наиболее универсальный и распространенный, используется в производстве автомобильных шин, резиновых шлангов и других резинотехнических изделий (рис. 9). Каучуки СКС характеризуются высокой морозостойкостью (до -77°С).
SKI — изопреновый каучук. Промышленно производятся следующие каучуки СКИ-3 для производства шин, амортизаторов; СУИ-3Д — для производства электроизоляционных резин; СКИ-3В — для вакуумной технологии (рис. 10).
Рис. 10. Вакуумный выключатель (а), электрозащитные перчатки (б)
SKH — Нитрил-бутадиеновый каучук. В зависимости от содержания нитрила акриловой кислоты нитрил-бутадиеновые каучуки можно дополнительно разделить на следующие марки СКН-18, СКН-26, СКН-40. Они устойчивы к воздействию бензина и нефтяных масел. На основе SKN Они устойчивы к бензину и нефтяным маслам; на их основе производятся резины для топливных и масляных шлангов, прокладок и мягких уплотнений топливных баков (рис. 11).
Натуральный и синтетический каучук — в чем разница?
Основное различие между натуральным каучуком и его синтетическим аналогом заключается в том, что натуральный каучук — это полимер природного происхождения, получаемый из млечного сока дерева под названием Hevea (Hevea brasiliensis). Синтетический каучук — это искусственно полученный полимер.
Синтетический каучук — это искусственно полученный полимерный материал, который по своим свойствам и характеристикам во многом копирует натуральный каучук. Этот материал получают путем полимеризации бутадиена, изопрена, стирола, изобутилена и других соединений. Синтетические каучуки состоят из длинных разветвленных молекулярных цепей с двойными связями.
Наиболее распространенным видом синтетического каучука является изопреновый каучук. Этот материал по своим свойствам и молекулярной структуре максимально приближен к натуральному каучуку. Именно изопреновый каучук нашел широкое применение в производстве шин (часто в сочетании с другими каучуками).
Свойства и характеристики резины
Резина представляет интерес благодаря своей гибкости. Этот универсальный материал способен претерпевать большие обратимые деформации при различных температурах. Свойства и характеристики каждого вида резины зависят от типа каучука, из которого она изготовлена. Свойства каучука могут значительно отличаться при использовании различных исходных материалов, пропорций, рецептур или модификаций.
В целом, резина обладает следующими уникальными свойствами
- эластичность
- способность поглощать удары и вибрации
- низкая теплопроводность
- высокая механическая прочность
- износостойкость
- устойчивость к воздействию газов и воды
- устойчивость к агрессивным средам
Резина является хорошим диамагнетиком и диэлектриком. Существуют специальные сорта резины, которые проводят электричество. Срок службы резиновых изделий может длиться десятилетиями.
История внешнего вида
Проблема заключалась в том, что гибкая резина становилась твердой после обработки. Только в 1823 году были найдены метод и пропорции ингредиентов, обеспечивающие сохранение гибкости. В то время примитивный каучук начали использовать для пропитки тканей, чтобы сделать их водонепроницаемыми.
Полноценный каучук впервые был получен только в 1839 году, когда была разработана технология вулканизации. Новый материал сразу же получил признание и стал использоваться для изготовления прокладок и изоляции.
Состав каучука
Чтобы получить каучук, его необходимо полимеризовать, но не простым нагреванием, а с добавлением серы. Созданная при этом среда обеспечивает вулканизацию, в результате чего масса становится не твердой, а эластичной.
Образующееся при этом вещество уже является каучуком, но совсем не тем, что мы называем сегодня. Он имеет мутный цвет, который трудно определить, очень восприимчив к эффекту старения и имеет много других недостатков. Чтобы улучшить его, оригинальная рецептура была усовершенствована.
Теперь он содержит:
Регенерат — это переработанный материал. Почти вся резина, за исключением высококачественных медицинских и подобных изделий, уже содержит использованные резиновые изделия. Их наличие снижает необходимую концентрацию каучука, который является самым дорогим компонентом состава.
Сера обычно используется в качестве вулканизирующего агента. Она содержится в количестве 1-35%. И от ее количества зависит уровень эластичности. В самых тяжелых случаях оно составляет всего 1-4%. Процесс вулканизации довольно трудоемкий. Чтобы ускорить его, используются добавки, обычно каптакс или оксид свинца. Необходимо очень небольшое количество — от 0,5 до 2%. Они не только действуют как ускорители, но и снижают температуру вулканизации.
Современная резина не является чистой вулканизационной резиной. Он состоит из различных наполнителей, которые могут составлять до 80%. Свойства резины зависят от того, какой из них используется.
Всего используется 3 различных типа наполнителей:
В качестве активного наполнителя используется технический углерод или свинцовые белила. Такие наполнители усиливают резину, делая ее более прочной, но в то же время позволяют ей сохранять некоторую степень эластичности. Они делают ее более устойчивой к разрывам и истиранию. Автомобильные шины являются ярким примером резины, изготовленной с использованием сажи.