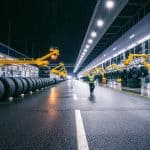
Из чего делают резину
(7 Голоса, значения: 4,86 z 5)
История появления
Вся проблема заключалась в том, что эластичный каучук после обработки становился твердым. Только в 1823 году был найден способ и пропорции ингредиентов, позволяющие ей сохранять свою эластичность. Именно тогда примитивный каучук начали использовать для пропитки тканей, чтобы сделать их водонепроницаемыми.
Полноценный каучук впервые был получен только в 1839 году, когда была разработана технология вулканизации. Новый материал сразу же получил признание и стал использоваться для прокладок и изоляции.
Состав каучука
Чтобы получить резину, каучук необходимо полимеризовать, но не простым нагреванием, а с добавлением серы. Создаваемая ею среда способствует вулканизации, делая массу не твердой, а эластичной.
Полученный в результате этого процесса материал уже является каучуком, но совсем не в том виде, в котором он известен сегодня. Он имеет мутный цвет, который трудно определить, очень восприимчив к эффекту старения и имеет много других недостатков. Чтобы улучшить его, оригинальная рецептура была усовершенствована.
Теперь он содержит:
Регенерат — это переработанный материал. Почти вся резина, за исключением высококачественных медицинских и подобных изделий, уже содержит использованные резиновые изделия. Их наличие снижает необходимую концентрацию каучука, который является самым дорогим компонентом состава.
Сера обычно используется в качестве вулканизирующего агента. Она содержится в количестве 1-35%. И от ее количества зависит уровень эластичности. В самых тяжелых случаях оно составляет всего 1-4%. Процесс вулканизации довольно трудоемкий. Чтобы ускорить его, используют добавки, чаще всего каптакс или оксид свинца. Эти добавки необходимы только в очень небольшом количестве — от 0,5 до 2%. Они не только действуют как ускоритель, но и снижают температуру вулканизации.
Современная резина не является чистой вулканизированной резиной. Он состоит из различных наполнителей, доля которых может достигать 80%. Свойства каучука зависят от того, какой из них используется.
Всего используется 3 типа наполнителей:
В качестве активного наполнителя используется технический углерод или свинцовые белила. Такие наполнители армируют резину, делая ее более прочной, но в то же время позволяют ей сохранять некоторую степень эластичности. Они делают ее более устойчивой к разрывам и истиранию. Автомобильные шины являются ярким примером резины, изготовленной из сажи.
Что такое резина?
Вы, конечно, знаете, что основным ингредиентом резины является каучук — натуральный материал, получаемый из каучуковых деревьев. Эти деревья растут в южной Африке очень давно, и трудно подсчитать их возраст. Однако европейцы познакомились с ними в 16 веке, когда Христофор Колумб вернулся на свою родину.
Если мы разложим слово ‘КАУЧУК’ на составные части, то получим ‘КАУ’ — растение, дерево, ‘УЧУ’ — плакать, течь. То есть, если переводить буквально, то это ‘плачущее дерево’, с языка индейцев Амазонии. Однако есть и научное название — ‘КАСТИЛЛА’, она растет на берегах Амазонки в непроходимых джунглях.
‘КАСТИЛЛА — очень высокое дерево, вырастающее до 50 м в высоту, цветущее круглый год. Кожура, листья и соцветия очень богаты так называемым млечным соком, который содержит натуральный каучук. Поскольку эти деревья очень большие, ветви или цветы часто отламываются, и дерево ‘выплакивает’ такой сок в месте поломки.
Вторым по величине деревом, содержащим этот сок, является дерево ГЕВАЙЯ, которое также вырастает до 40-50 метров. Когда оно достигает возраста 9-10 лет, на его стволе делают V-образные надрезы, из которых начинает сочиться натуральный каучук. При контакте с воздухом он становится липким.
Это два основных растения, из которых получают натуральный каучук. В Центральной Азии, а также на побережье Южной Америки, в Бразилии, Перу и на острове Шри-Ланка, существуют целые плантации таких деревьев, которые существуют только для одной цели — добывать этот сок! Это хорошо развитый бизнес.
В пятерку ‘популярных’ растений также входят кустарники МАНИОКА, СОЛНЕЧНОЕ ДЕРЕВО и ИН-ЦИ. Все они являются источниками для последующего производства каучука.
Производство каучука
И вот мы подошли к самой интересной части — производству самой резины, не обязательно автомобильных колес, в наши дни резина используется везде, даже в резинке для волос.
После сбора каучукового сока предстоит пройти долгий путь производства каучука. Первоначально он используется для производства латекса, который является промежуточным продуктом. Однако чистый латекс сегодня используется повсеместно — от медицины до промышленности.
Сок выливают в большие чаны и перемешивают в них с кислотой, обычно в течение 10 часов. Затем он затвердевает. Это то, что делает латекс.
Затем его пропускают через специальные валики, удаляя таким образом лишнюю влагу. В результате получается достаточно длинная и широкая лента.
Такую ленту пропускают под специальными ножами и измельчают. Если посмотреть на эту смесь, то она напоминает пережаренный омлет.
Эту воздушную массу выпекают в больших духовках при достаточно высокой температуре — 13 минут. Теперь она получается податливой и напоминает бисквит, ее прессуют в блоки и отправляют на производство.
Конечно, точную формулу изготовления резины, а тем более шин, вы не найдете — все это держится в строжайшем секрете. Однако суть процесса не изменилась за последние 100 лет и хорошо известна всем.
Для производства каучука берут брикеты латекса и вулканизируют их. Также добавляется сера и другие ‘скрытые’ ингредиенты. Все это добавляется в специальный котел, нагревается, перемешивается, и после таких манипуляций уже появляется резина.
Как только она нагревается до 120 градусов, ее раскатывают специальными валиками в тонкие полоски. Там она также охлаждается.
Разница между резиной и силиконом заключается в следующем.
- термостойкость: силиконовые изделия сохраняют свою структуру и функциональные свойства при температуре от -100 °C до +300 °C, в то время как компоненты из термопластичной резины выдерживают температуру от -40 °C до +120 °C;
- устойчивость к атмосферным агентам;
- устойчивость к агентам биологического происхождения (к вредным микроорганизмам, насекомым и грызунам).
Кроме того, силикон обладает лучшими свойствами на растяжение и растрескивание, чем резина, при одинаковых температурах и более длительным сроком службы.
Что касается преимуществ резины перед силиконом, то стоит отметить ее значительно более низкую стоимость.
Как отличить силикон от резины
Как узнать, из какого материала был изготовлен тот или иной продукт?
- PomnиРастяните материал во всех направлениях. Силикон податлив и мягок, а резина более твердая.
- Если вы не удовлетворены результатами первого теста, переходите ко второму. Подожгите край изделия (если, конечно, это не ремешок для обуви или часов, а, например, одно уплотнительное кольцо из целой партии) и понаблюдайте за ‘поведением’ материала. Резина начнет плавиться и издавать резкий запах, почернеет в месте контакта с пламенем, в то время как силикон будет вести себя более ‘мягко’, образуя легкие хлопья пепла и выпуская белый дым.
Чтобы убедиться в этом, можно провести третий тест, просто поместив изделие в морозильную камеру на 10-15 минут. Структура силикона не изменится, а резина затвердеет.
Заключение
Автомобильная резина в основном состоит из следующих компонентов
- резина;
- смолы;
- кремниевая кислота;
- технический углерод;
- секретные химические элементы, добавляемые в резину для придания ей определенных свойств (мел, глицерин, ацетилированный ланолин и т.д.).
Качество готового продукта зависит от качественных и количественных характеристик этих ингредиентов. Не поддавайтесь влиянию рекламы и не отдавайте предпочтение шинам, изготовленным с использованием новых химических компонентов. Перед покупкой таких шин поинтересуйтесь, соответствуют ли заявленные производителем шины параметры действительности.
Читайте другие статьи на эту тему:
Камуфляж важнее всего
С кремнеземом, однако, есть проблемы. В химии существует правило, что он в ней растворяется. К сожалению, каучуки и другие полимеры совсем не похожи на кремнезем в химическом отношении, точку соприкосновения можно сравнить с несмешивающимися маслом и водой.
Это означает, что при простом смешивании ингредиентов вы получаете отдельно большие липкие комки наполнителя и отдельно блоки резины, в которых нет наполнителя. В процессе сжатия-растяжения наполнитель будет трескаться и ломаться, на это будет затрачиваться дополнительная энергия, что означает увеличение трения качения.
Но и здесь есть решение. Чтобы масло смешивалось с водой, образуя эмульсию (например, молоко), нужны поверхностно-активные вещества, такие как мыло.
То же самое верно и для шин — вам нужно вещество, которое может покрыть поверхность кремнезема и ‘замаскировать’ ее под окружающие полимеры. Такими веществами являются, например, бис-(триэтоксисилилпропил)тетрасульфид и его аналоги. Их молекулы состоят из двух частей, одна из которых легко связывается с диоксидом кремния, а другая — с решеткой вулканизированного полимера.
Даже имея такой практически идеальный ‘маскирующий агент’, нельзя обойтись без надежной технологии его распределения по поверхности частиц. Если маскирующих частиц слишком мало, частицы диоксида кремния все равно слипнутся. К сожалению, молекулы маскирующего агента способны к агрегации — они не сцепляются с поверхностью частиц. Чтобы противостоять этому, компания Toyo Tires, например, использует специальную технику точного смешивания — контролируя соотношение различных компонентов в смеси. Это основано на возможности отслеживать скорость реакции между маскирующим агентом и кремнеземом.
По оценкам шинной промышленности, с 1890-х годов трение качения снизилось примерно на треть благодаря добавкам и изменениям в конструкции колес.
Добавление диоксида кремния, по сравнению с классической сажей, также увеличивает сцепление на мокрой дороге. Все дело в том же принципе ‘подобное растворяется подобным’.
На микроскопическом уровне
Свойства готовой шины, как уже известно, зависят не только от массовых долей добавок, но и от их распределения в резине. Чтобы сверить свойства готовых шин с прогнозами моделей Toyo Tires, компания обратилась к синхротронному излучению для изучения деформации материалов на наноуровне.
Синхротронное излучение — это тип рентгеновского излучения, производимого ускорителями частиц. Благодаря короткой длине волны это излучение легко проникает через тонкую пластину резиновой смеси, оставляя на детекторе тени на месте частиц наполнителя. Высокая интенсивность излучения позволяет записывать ‘пленки’ об — изменений, происходящих в микро- и наноструктуре образца за доли секунды.
Таким образом, впервые в шинной промышленности компания получила синхротронные данные о том, как ведут себя частицы наполнителя, равномерно и неравномерно распределенные в резиновой смеси. В последнем случае при динамических нагрузках возникают дополнительные потери энергии.
Тщательно отслеживая химический состав и микроскопическое поведение резиновых смесей, ученые и инженеры все ближе подходят к созданию идеального колеса. Каждое последующее поколение материалов позволяет набрать еще несколько процентов и немного расширить ‘магический треугольник’ свойств, делая шины более безопасными, надежными и эффективными.
Но возможности оптимизации шин на этом не заканчиваются; в следующий раз мы рассмотрим, как разработать правильный рисунок протектора и внутреннюю структуру.