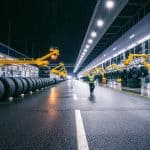
Химический состав каучука
В пятерку ‘популярных’ растений также входят МАНИОКА, СОЛНЕЧНОЕ ДЕРЕВО и кустарник ИН-ТИСИ. Все они являются источниками для последующего производства каучука.
Из чего состоят автомобильные шины
Еще одним важным элементом в составе шины является углерод, или, как говорят в народе, сажа. Он составляет примерно 30% смеси.
Для чего используется углерод? По сути, это элемент, который упрочняет состав, действуя на молекулярном уровне. Без сажи шины были бы недолговечными, хрупкими и склонными к чрезмерному износу.
Сегодня вместо технического углерода чаще всего используется сера. Но выбор того или иного ингредиента — это скорее вопрос доступности. С научно-технической точки зрения разница невелика.
Химический состав резины для автомобильных шин
Заменителем технического углерода является кремниевая кислота. Она используется в качестве заменителя технического углерода в связи с тем, что последний постоянно дорожает. Однако это решение вызывает некоторые споры среди экспертов, поскольку кремниевая кислота обладает меньшей износостойкостью и большим сцеплением на мокрой дороге. Другими словами, она теряет износостойкость, но приобретает лучшее сцепление.
В качестве добавок к смеси используются различные масла и смолы. Они оказывают смягчающее действие, что особенно важно при производстве зимних шин.
Тот факт, что резина содержит кремниевую кислоту, кукурузный крахмал или другие заявленные добавки, ничего не значит. Самое главное — придумать хороший рецепт, а потом не нарушить этот самый рецепт, который при наличии этих ингредиентов дал бы идеальную автомобильную шину. А это удается далеко не всем производителям. Поэтому то, как производят шины разные производители, является тщательно охраняемым секретом.
Вкратце можно сказать, что автомобильные шины изготавливаются либо из резины, либо из других материалов, но с добавлением резины. Производители шин имеют свой оптимальный химический состав, который определяет различные свойства получаемой резины.
Один производитель делает упор на долговечность, другой — на скоростные свойства, третий — на поведение шины на мокрой дороге. Эти свойства определяют цену и качество шины. Кроме того, для придания шине упругости, прочности и износостойкости в нее добавляют алюминиевые корды, нейлоновые волокна и различные добавки.
Как проводится анализ резины?
Обычно на анализ поступает цельный кусок резины, в редких случаях анализируется участок изделия. В этом случае образцы берет специалист, который выезжает на место и берет соскоб. Важно правильно выбрать материал для тестирования, чтобы получить наиболее точные результаты.
Затем образец помещается в специальный контейнер, хранится при оптимальных условиях хранения и транспортировки и доставляется в лабораторию, где проводятся испытания физического и химического состава.
С помощью физических испытаний определяются такие свойства резины, как стойкость к истиранию, пластичность, прочность на разрыв, электрические свойства, устойчивость к перепадам температур и другие параметры.
Химический анализ используется для определения состава резины и количества компонентов. С его помощью определяется соответствие требованиям ГОСТа и определяется сорт резины. Идентификация Анализ резины позволяет идентифицировать производителя и выявить контрафактную продукцию. Для этого необходимо предоставить на анализ исходный образец и сам материал.
Где заказать анализ?
Для того чтобы быть уверенным в том, что результаты анализа легитимны и могут быть использованы в качестве доказательства в суде по арбитражным, гражданским и уголовным делам, необходимо обратиться в сертифицированную лабораторию. Наш центр химического анализа является одной из них. Мы сертифицированы Палатой судебных экспертов, поэтому заключения, которые мы выдаем, имеют силу закона и принимаются следственными органами и судами всех инстанций.
Стоимость исследования в нашей независимой лаборатории рассчитывается индивидуально, с учетом конкретных данных, таких как объем исследуемого образца, выбранный метод анализа, сложность тестов, количество вопросов, поставленных перед экспертом.
Заказать анализ резины в нашей химической лаборатории можно заказать по телефону, либо заполнив форму обратной связи на сайте.
Заявка kipmu.ru
Каучук — это натуральное сырье, состоящее из химических соединений, которые, вступая в химическую реакцию с добавками, улучшают свойства вторичного продукта (резины). В результате получается вязкий, устойчивый к агрессии материал с более длительным сроком службы. Резина может сохранять свои качественные характеристики в широком диапазоне температур.
Резина быстро стареет под воздействием окислителей и кислорода. При низких температурах она становится хрупкой и теряет эластичность, а при высоких температурах разлагается. Таким образом, резина обладает наилучшими свойствами, но обязана ими каучуку.
Если вы нашли ошибку, выделите текст и нажмите клавиши Ctrl+Enter.
Натуральный каучук
Натуральный каучук — это сок некоторых растений, каучуконосНекоторые из них включают травы, деревья и лианы.
Натуральный каучук часто приравнивают к латексу. Латекс представляет собой эмульсию дисперсных полимерных частиц в водном растворе: в природе он встречается в виде млечного сока различных растений. Однако существует только один вид латекса на основе натурального каучука (NR): концентрированный и стабилизированный млечный сок бразильского растения гуава. С помощью центрифугирования или отстаивания содержание сухого вещества в латексе искусственно увеличивается до 75 % (в исходном соке содержится в среднем около 40 %).
История открытия натурального каучука
С тех пор каучук стал важнейшим ингредиентом промышленного производства во всем мире.
Как получают каучук: растение натурального каучука
Наиболее известными деревьями натурального каучука являются деревья рода Hevea, в частности бразильская Hevea. Половина сока этого дерева состоит из каучуковых веществ. На втором месте находится Ficus rubberus (он же Ficus elastica). На третьем месте — несколько сортов одуванчиков (кок-сагыз, тау-сагыз, крым-сагыз). Одуванчики содержат натуральный каучук в своих корневищах, сухой вес которых достигает 15%. Максимальное количество каучука в кок-сагызе — 27,55%.
Каучук добывают различными методами. Самый старый метод, который используется и сегодня, — это метод косого глаза. Он предполагает сбор млечного сока деревьев (латекса) путем надрезания коры. Процесс сбора занимает много времени, поскольку сок вязкий и собирается медленно. Из латекса каучук коагулируют органическими кислотами, промывают водой и скатывают в листы, которые сушат и коптят дымом. Копчение защищает каучук от окисления и воздействия микроорганизмов. Добыча каучука из корней растений одуванчика-сагыза осуществлялась иначе — растения собирали, сушили и перерабатывали в массе. Этот метод был популярен в Советском Союзе как альтернатива труднодоступному латексу из гевеи.
Синтетические каучуки
Синтетические каучуки — это группа эластичных веществ, получаемых в результате реакции полимеризации и сополимеризации диеновых углеводородов с сопряженными двойными связями. Синтез каучуков стал необходимостью в связи с нехваткой сырья для производства натурального каучука. Синтетические каучуки также могут быть переработаны в резину путем вулканизации.
История открытия синтетического каучука
Производство синтетических каучуков стало насущной необходимостью с развитием промышленности. Эксперименты Майкла Фарадея по изучению химического состава и структуры каучука и его синтезу из несельскохозяйственного сырья дали начало этой тенденции. Синтетический каучук был открыт в 1879 году французским химиком Г. Бушаром. Он обработал изопрен (2-метилбутадиен-1,3) соляной кислотой и получил вещество со свойствами каучука.
Большой вклад в развитие производства синтетического каучука внесли русские химики: в 1901 году И. Кондаков синтезировал эластичный полимер из диметилбутадиена, после чего были получены промышленные партии синтетического каучука (диметилкаучука). Однако диметилкаучук не получил широкого распространения, и его производство было прекращено.
Первое в мире крупномасштабное производство синтетического каучука начал российский химик С.В. Лебедев. Лебедев. В 1910 году он первым произвел синтетический бутадиеновый каучук и бутадиен-натриевый каучук. Лебедев и его коллеги успешно разработали недорогой и эффективный метод: одностадийный способ получения бутадиена из этилового спирта на смешанном цинк-алюминиевом катализаторе: 2CH3CH2OH® 2H2O + CH2=CH-CH=CH2 + H2. Натриевый бутадиеновый каучук получают при использовании металлического натрия в качестве катализатора полимеризации бутадиена.
Формула, состав и структура синтетического каучука
Синтетический каучук производится путем полимеризации стирола, неопрена, бутадиена, изобутилена, хлоропрена, нитрила акриловой кислоты.
Реакция каучука зависит от выбранного метода производства. Например, стирол-бутадиеновый каучук получают путем сополимеризации бутадиена со стиролом по реакции с использованием не одного, а двух различных мономеров:
Основные свойства базового синтетического каучука.
Каучук NBR (акрилонитрил-бутадиен)
Это смешанный полимер с содержанием акрилонитрила 18-50%. Чем больше акрилонитрила в составе материала, тем выше стойкость готового изделия к нефтепродуктам и маслам, но тем ниже эластичность и остаточная деформация при сжатии. Как правило, по его содержанию в резиновой смеси приходится идти на компромисс. Старение ускоряется при повышении рабочей температуры, но в маслах оно происходит медленнее, чем в горячем воздухе.
Несомненными преимуществами NBR перед другими материалами являются его отличные механические свойства и высокая износостойкость. Недостатками являются устойчивость к озону и атмосферным воздействиям.
- алифатические углеводороды;
- минеральные масла, нефтяные масла, смазки;
- растительные жиры, животные жиры;
- дизельное топливо, мазут;
- жидкости HFA, HFB, HFC;
- Разбавленные кислоты, щелочи, соляные растворы (при низких температурах);
- Вода (до +100°C для специальных резиновых смесей).
- Ароматические углеводороды (бензол и т.д.), а также топливо с их высоким содержанием (высокооктановый бензин);
- хлорированные углеводороды;
- сильные кислоты;
- озон;
- тормозные жидкости на основе гликоля;
- полярные растворители (ацетон, другие кетоны, этиленовый эфир, уксусная кислота).
HNBR — гидрогенизированный нитрил-бутадиеновый каучук
Модификация NBR, полученная путем гидрогенизации. По сравнению с NBR, материал более устойчив к окислению и высоким температурам и обладает превосходными физико-механическими свойствами. HNBR устойчив к атмосферным воздействиям.
Полибутадиеновый каучук повышает эластичность и стойкость резины к истиранию. Поэтому в большинстве случаев он используется в качестве ингредиента в резиновых смесях на основе других полимеров для улучшения их эксплуатационных свойств. Как основа БР он используется в производстве конвейерных лент, приводных ремней. В отличие от этого, ‘чистые’ бутадиеновые резиновые смеси не подходят для производства прокладок.
Физические и химические свойства основных марок синтетического каучука
Синтетический каучук | Температурная стойкость | Сохраняет гибкость при отрицательных температурах | Химически устойчив к следующим средам: | Не устойчив к следующим средам: |
---|---|---|---|---|
NBR | До +100 °C (со снижением прочности до +120 °C) | -20…-55 °C (в зависимости от смеси) | Алифатические углеводороды, разбавленные кислоты и основания, масла, нефтепродукты | Ароматические и хлорированные углеводороды, озон, растворители |
IIR | До +130 °C | -40 °C | Вода, кислоты, полярные растворители, силиконовые масла, озон | Хлорированные углеводороды, минеральные масла, нефтехимические продукты |
CR | +100 °C (+120 °C) | -40 °C | Минеральные и силиконовые масла, хладагенты, аммиак, озон | Хлорированные и ароматические углеводороды, ацетон, сложные эфиры |
CSM | До +120 °C | -30 °C | Силиконовые масла, кислоты, щелочи, озон | Хлорированные и ароматические углеводороды |
ECO, CO | До +135 °C | -40 °C | Минеральные и силиконовые масла, топливо, алифатические углеводороды, озон | Ароматические и хлорированные углеводороды, полярные растворители, гликолевые тормозные жидкости |
AEM | До +150 °C (временно до +175 °C) | -30…-40 °C | Минеральные масла, озон, кислород | Топливо, кетоны, тормозные жидкости |
EPM, EPDM | До +150 °C (в воде и паре до +180 °C) | -50 °C | Кислоты, щелочи, силиконовые масла, смазки, полярные растворители, озон | Минеральные масла, смазки, топливо |
FKM | До +200 °C (и более при сокращении срока службы) | -25 °C (специальные смеси до -50 °C) | Топливо, пропан, бутан, природный газ, бензол, толуол, хлорированные углеводороды, кислород, озон, минеральные масла | Полярные растворители, гликолевые тормозные жидкости, основания, уксусная и муравьиная кислоты, перегретый пар |
LSR, VMQ, MQ, Q | До +210 °C (некоторые марки до +230 °C) | -55…-60 °C (специальные марки до -100 °C) | Гликолевые тормозные жидкости, смазки, клофен, хлордифенил, слабые солевые растворы, озон | Трихлорэтилен, бензол, толуол, перегретый пар, кислоты, щелочи, силиконовые масла, топливо |
FVMQ | +175 °C (+200 °C) | -55 °C | Гликолевые тормозные жидкости, жиры, клофен, хлордифенил, слабые солевые растворы, озон, ароматические углеводороды, минеральные масла, топливо | Трихлорэтилен, пар, кислоты, щелочи, силиконовые масла |
HNBR | Температурный диапазон до +150 °C | -40 °C | Алифатические углеводороды, жидкости HFA, HFB, HFC, растительные масла, животные жиры, вода, перегретый пар, озон, разбавленные кислоты, щелочи, соли | Ароматические и хлорированные углеводороды, растворители |
FFKM | До +310 °C | -15…35 °C | Практически все агрессивные и неагрессивные химические вещества, включая кислород и озон | Фторсодержащие соединения (например, некоторые ХФУ) |
ACM | До +150 °C (временно до +175 °C) | -20 °C | Минеральные масла (моторное масло, ATF, ATF), озон, кислород | Тормозные жидкости на основе гликоля, ароматические и хлорированные углеводороды, кислоты, щелочи, горячая вода, пар, амины |
SBR | +100 °С | -50 °C | Гликоли, ацетон, силиконовые масла, смазочные материалы | Минеральные масла, топливо, алифатические и хлорированные углеводороды, окислители |